目次
レーザー鋼溶接機の原理
鋼溶接機 今日最も人気のある溶接機です。 このレーザー溶接機は様々な分野で使用されていますが、レーザー溶接機の原理をご存知ですか? レーザー溶接アルミニウム機は、高強度のレーザービームを金属表面に放射し、レーザーと金属の相互作用により、金属を溶かして溶接を形成します。 レーザーと金属の相互作用の過程で、金属の融解は物理現象のXNUMXつにすぎません。
時間エネルギーは主に金属の融解に変換されない場合がありますが、気化やプラズマ形成などの他の形で現れます。 ただし、良好な融接を実現するには、金属溶融がエネルギー変換の主な形態である必要があります。 このため、レーザーと金属の相互作用によって生じるさまざまな物理現象と、これらの物理現象とレーザーパラメーターの関係を理解する必要があります。 レーザーパラメータを制御することにより、レーザーエネルギーのほとんどを金属溶融エネルギーに変換して溶接を実現できます。 目的。
これが理由です レーザー溶接機 とても暖かく歓迎されています。 この溶接機は、元の通常の溶接機よりも効率的であり、すべての材料をよりよく溶接することができます。
レーザー鋼溶接機のプロセスパラメータ
他の溶接機と比較して、レーザー溶接アルミニウム機のプロセスパラメータは非常に高いです。 レーザー溶接機は、出力密度、レーザーパルス波形、レーザーパルス幅、および焦点ぼけの点で非常に優れた性能を発揮します。 。
1.電力密度
電力密度は、の処理において最も重要なパラメータのXNUMXつです。 ステンレス鋼溶接機。 より高い電力密度では、マイクロ秒の時間範囲内で表面層を沸点まで加熱することができ、その結果、大量の気化が生じます。 したがって、高出力密度は、パンチング、切断、彫刻などの材料除去処理に役立ちます。 電力密度が低い場合、表面温度が沸点に達するまでに数ミリ秒かかります。 表層が気化する前に、下層が融点に達します。これにより、良好な融接が容易に形成されます。 したがって、導電性レーザー溶接では、出力密度は104〜106W / cm2の範囲になります。
2.レーザーパルス波形
レーザーパルス波形は、 鋼溶接機、特にシート溶接用。 高強度のレーザービームが材料の表面に当たると、レーザーエネルギーの60〜98%が金属表面で反射および失われ、反射率は表面温度によって変化します。 レーザーパルスの間、金属の反射率は大きく変化します。
3.レーザーパルス幅
パルス幅は、アルミニウム溶接機のレーザー溶接の重要なパラメータのXNUMXつです。 これは、材料の除去や材料の溶解とは異なる重要なパラメータであるだけでなく、処理装置のコストと量を決定する重要なパラメータでもあります。
4.デフォーカス量が溶接品質に及ぼす影響
レーザーステンレス鋼溶接機は、レーザー焦点のスポットの中心のパワー密度が高すぎて、穴に蒸発しやすいため、通常、ある程度の焦点ぼけが必要です。 レーザー焦点から離れた各平面では、パワー密度分布は比較的均一です。
焦点ぼけには、正の焦点ぼけと負の焦点ぼけのXNUMXつの方法があります。 焦点面がワークピースの上にある場合、それは正の焦点ぼけです。そうでない場合、それは負の焦点ぼけです。 幾何光学理論によれば、正と負の論理和が等しい場合、対応する平面の電力密度はほぼ同じですが、実際には、得られる溶融池の形状が異なります。
デフォーカスが負の場合、より深い侵入深さを得ることができ、これは溶融池の形成プロセスに関連している。 実験によると、材料の50〜200usのレーザー加熱が溶け始め、液体金属を形成して気化し、都市圧力蒸気を形成し、非常に高速で噴霧して、まばゆいばかりの白色光を放出します。
同時に、蒸気の濃度が高いと、液体金属が溶融池の端に移動し、溶融池の中央にくぼみが形成されます。 デフォーカスが負の場合、材料の内部パワー密度は表面のパワー密度よりも高く、より強い融解と気化を形成しやすいため、光エネルギーを材料のより深い部分に伝達することができます。 したがって、実際のアプリケーションでは、侵入深さを大きくする必要がある場合は、負の焦点ぼけが使用されます。 薄い材料を溶接する場合は、正の焦点ぼけを使用する必要があります。
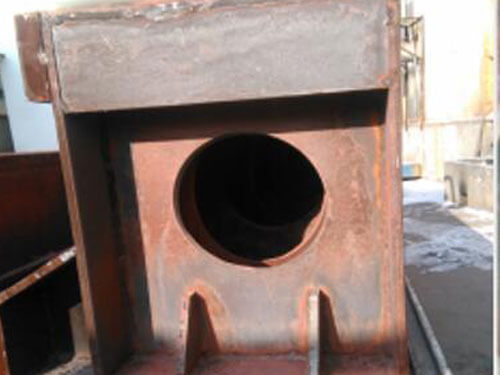
レーザー溶接アルミニウム機械プロセス法
最も人気のある溶接機として、 レーザー溶接アルミ機 さまざまな種類の材料を溶接でき、金属板やワイヤー、さまざまな金属など、さまざまな材料を溶接できます。 私たちの鋼溶接機は溶接することができます。
1.スライス間の溶接:XNUMXつのプロセス方法を含みます:突合せ溶接、端部溶接、中心溶け込み融接、中心穿孔融接。
2.ワイヤーおよびワイヤー溶接: ワイヤーツーワイヤー突合せ溶接、クロス溶接、平行重ね溶接、T字型溶接およびその他の4つのプロセス方法を含みます。
3.金属ワイヤーとブロックコンポーネントの溶接: レーザー溶接は、金属線とブロック要素の接続をうまく実現することができ、ブロック要素のサイズは任意にすることができます。 溶接中は、ワイヤー状のコンポーネントの幾何学的寸法に注意を払う必要があります。
4.さまざまな金属の溶接: さまざまな種類の金属を溶接することで、溶接性と溶接可能なパラメータの範囲を解決する必要があります。 異なる材料間のレーザー溶接は、特定の材料の組み合わせでのみ可能です。
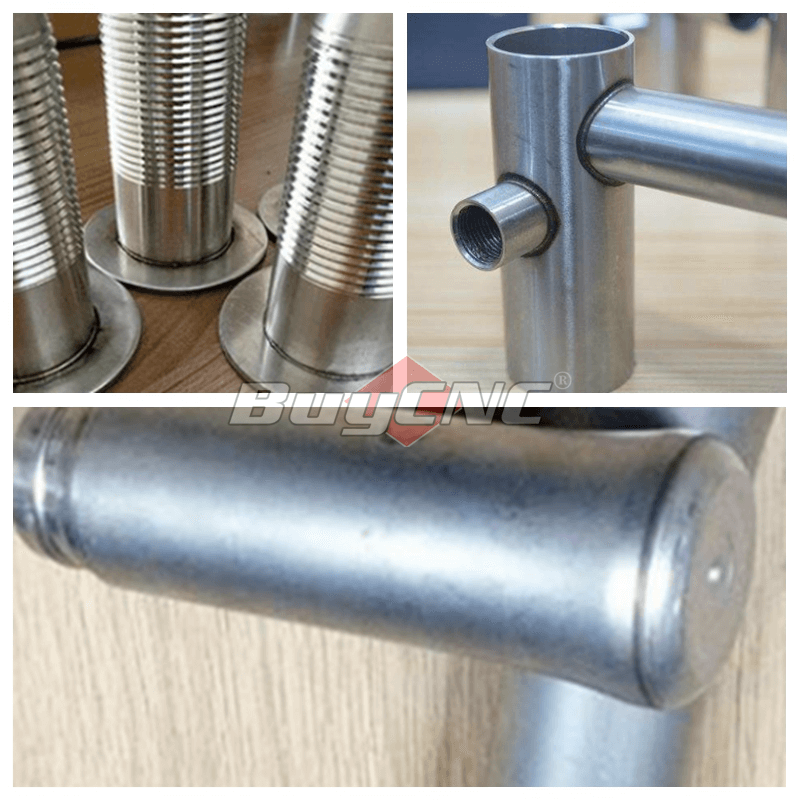
レーザーステンレス鋼溶接機の利点
他の溶接技術と比較して、 レーザー溶接アルミ機 多くの利点があるので、レーザー溶接アルミニウム機の主な利点は次のとおりです。
1.高速、深さ、変形が小さい。
2.室温または特別な条件下で溶接することができ、レーザーステンレス鋼溶接機は簡単です。 たとえば、レーザーが電磁場を通過するとき、ビームはシフトしません。 レーザーは、真空、空気、および特定のガス環境で溶接でき、ビームに対して透明なガラスまたは材料を介して溶接できます。
3.チタン、石英などの耐火材料を溶接でき、異種材料を溶接して良好な結果が得られます。
4.レーザーの焦点を合わせた後、出力密度が高くなります。 高出力デバイスを溶接する場合、アスペクト比は5:1、最大10:1に達する可能性があります。
5.マイクロ溶接が可能です。 レーザービームの集束後、小さなスポットを得ることができ、正確に配置することができます。これは、自動的に大量生産されるマイクロワークピースとスモールワークピースのアセンブリ溶接に適用できます。
6.アクセスしにくい部品を溶接でき、柔軟性の高い非接触遠距離溶接が可能です。 特に近年、YAGレーザー加工技術に光ファイバー伝送技術を採用することで、レーザー溶接技術の普及・応用が進んでいます。
7.レーザービームは、時間と空間に応じたビーム分割を実現しやすく、マルチビーム同時処理とマルチステーション処理が可能で、より精密な溶接条件を提供します。
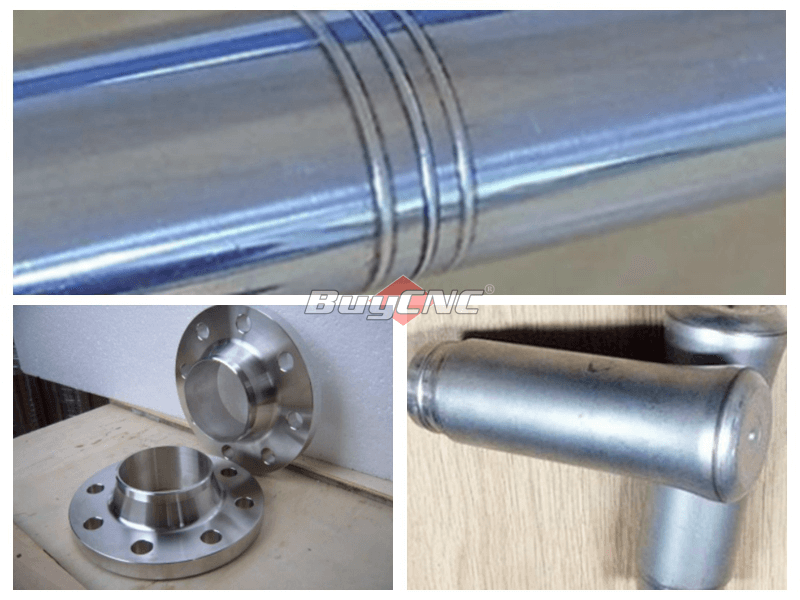
レーザー鋼溶接機のデメリット
ただし、レーザー溶接には特定の制限もあります。
1。 ザ レーザー溶接アルミ機 溶接物の組み立てには高精度が必要であり、ワークピース上のビームの位置が大幅にずれないようにする必要があります。 これは、レーザーの焦点を合わせた後、スポットサイズが小さく、溶接部が狭く、金属材料で満たされているためです。 ワークの組立精度やビームの位置決め精度が要件を満たしていない場合、溶接不良が発生しやすくなります。
2.レーザー溶接アルミニウム機が作動している場合、レーザー溶接機の最大溶接可能厚さはある程度制限されます。 19mmをはるかに超える厚さのワークピースを溶接する場合は、鋼製溶接機での溶接には適していません。
19つは、溶接部の位置が非常に正確で、レーザービームの焦点範囲内にある必要があるということです。 XNUMXつ目は、溶接部で固定具を使用する必要がある場合、溶接部の最終位置がレーザービームが衝突する溶接点と一致していることを確認する必要があることです。 XNUMXつ目は可能な限り最大の溶接厚さであり、溶け込み厚さがXNUMXmmをはるかに超えるワークは、生産ラインでのレーザー溶接には適していません。
3.レーザー溶接アルミニウム機とその関連システムのコストは比較的高いです。 通常の溶接機に比べて、レーザー溶接機のXNUMX回限りの投資は比較的大きい。
販売のためのレーザー鋼溶接機
